[ad_1]
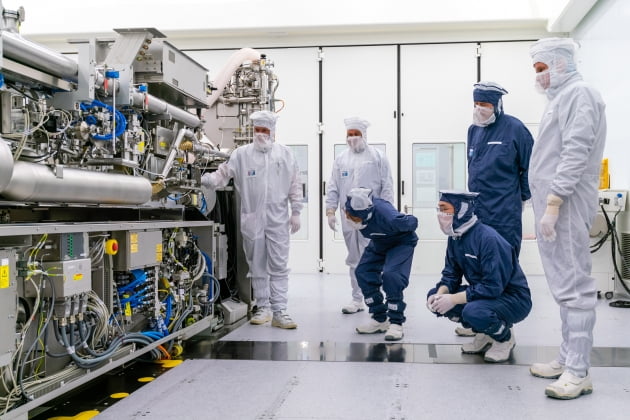
Samsung Electronics Vice President Lee Jae-yong (fourth from left) visited ASML headquarters in Eindhoven, the Netherlands, on the 13th of last month to see the EUV equipment. Yunhap news
On the 13th of last month, Samsung Electronics Vice President Lee Jae-yong, dressed in a dustproof suit, squatted down and looked at a computer in focus (photo) became a hot topic. This is an image showing ‘extreme ultraviolet (UEV) equipment’ at the headquarters of ASML, a Dutch semiconductor equipment company.
EUV equipment is necessary for one of the semiconductor production processes, the exposure process (work that etches a circuit on a wafer, which is an original semiconductor board as if taking a photograph). The light is used to record the circuit, and the wavelength (13.5 nm, nm = 1 billionth of a meter) uses extreme ultraviolet, which is a 14th of the existing equipment (193 nm). If the wavelength of the light is short, it is possible to accurately draw a semiconductor circuit on the wafer. It is similar to being able to make more elaborate drawings with a fine brush than with a thick brush.
Order now and arrive in 18 months
18 months. Now, if Samsung Electronics, SK Hynix and Taiwan TSMC order EUV equipment from ASML, it will take time to receive it. Although it’s an ultra-high-priced piece of equipment costing 150 billion won per unit, orders are overdue. Recently, there has been competition among semiconductor companies to make small semiconductors with good energy efficiency, because EUV equipment is essential for this.
One of Vice President Lee’s main goals on his trip to Europe was to smoothly supply EUV equipment. Currently, TSMC, the world’s number one foundry (semiconductor consignment production), is estimated to have 50 units, and Samsung Electronics has around 10 EUVs. As Samsung Electronics started using EUV not only for foundries but also for DRAM production, the need increased. It is enough to create a “UEV team” in the company.
But even if you want to buy it, you can’t. This is because the number of EUV kits ASML can produce per year is 35 units as of this year. This is also an increase of 9 units over last year (26 units).
The equipment that is being shipped now was most likely ordered by semiconductor companies about a year and a half ago. In the semiconductor industry, the majority of EUV equipment released this year is said to have been for TSMC. It is not known why Samsung Electronics is, but it is the reason why the analysis suggests that it would not have placed many orders for the equipment at ASML last year. Despite the new coronavirus infection (Corona 19), the reason why Vice President Lee will go to the ASML headquarters in the Netherlands can be predicted.
It took 20 weeks to build an EUV device
Why does it take so long to ask and receive? According to ASML, it takes 20 weeks to build an EUV device.
First of all, the scale of the team is large. An EUV team weighs 180 tons and occupies approximately the second floor of an apartment. If you connect some 3,000 connected lines in the equipment, the length alone is said to exceed 2km. It is said that to bring EUV equipment from the Netherlands to Korea, three aircraft are needed.
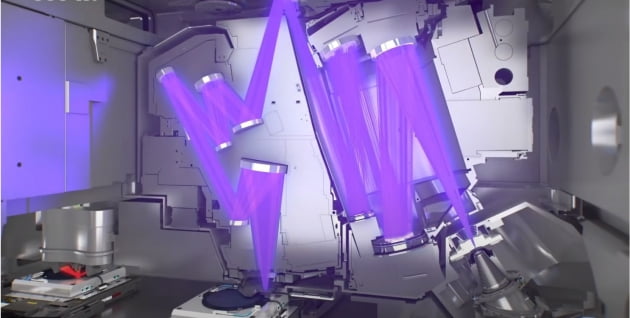
Inside the EUV exhibition team. Purple is an extreme ultraviolet ray and a silver round disk is a reflective mirror. ASML Home Page
It is not just a lot of accessories. The best semiconductor technology in the world is concentrated because ultrafine processing is performed at the nm level (one billionth of a meter). Some say that the precision required when drawing a circuit on a wafer with extreme ultraviolet rays is the level of hitting a coin on the moon by shooting light from the ground.
The space that plays a key role in the circuitry on the wafer by radiating extreme ultraviolet rays within the EUV equipment is called the “vacuum state”. Indoor air pressure is one hundred thousandth of the atmosphere, and there is a technology to control the temperature in units of 0.005 degrees. ASML took more than 20 years to develop and commercialize such EUV kits. Even ASML that has been successfully marketed is not at the level that can be done.
Carl Zeiss, which makes mirrors for EUV equipment, is a ‘super bottle’
For this reason, ASML is regarded as ‘Super E’ in the semiconductor industry. Although it is an equipment supplier, semiconductor manufacturers have no choice but to realize it.
However, there are several manufacturers of parts that ASML can only trust. One of them is Karl Zeiss, a German optics company famous for its camera lenses.

Carl Zeiss logo. Home page capture
The characteristic of the EUV equipment is that it uses extreme ultraviolet rays with a wavelength of 13.5 nm. Existing exposure equipment using light with a wavelength of 193 nm used a method of projecting light using a lens. However, extreme ultraviolet rays, which are the light sources of EUV equipment, have a short wavelength but have a disadvantage. The light is absorbed even when it only touches the air. Then, as described above, the interior is converted into a ‘void’ state and instead of a lens absorbing the light, a circuit is etched into the wafer using various specially manufactured ‘reflective mirrors’ to reflect the light. Carl Zeiss is the only place that can manufacture this reflective mirror.
It is said that it takes a long time to make this mirror. There are rumors that Carl Zeiss makes mirrors “ handcrafted ” by some.
‘Super bottle’ Carl Zeiss has a long association with ASML. A typical case is that ASML bought a 24.9% stake in Carl Zeiss SMT, the semiconductor business unit of Carl Zeiss, for 1 billion euros (about 1.3 trillion won). Like Samsung Electronics, which owns 1.5% of ASML, ASML also invested in Carl Zeiss for a long-term partnership. ASML is known to have invested around 1 trillion won in R&D to improve the performance of reflective mirrors in addition to the capital investment.
35 production units this year, 40-50 units next year
Will the need to wait 18 months to buy EUV equipment continue? ASML announced in a conference call (telephone performance briefing) in the third quarter of last year that “next year, 40 to 50 units of EUV equipment can be produced.” Less than this year, 5 more, 15 more.
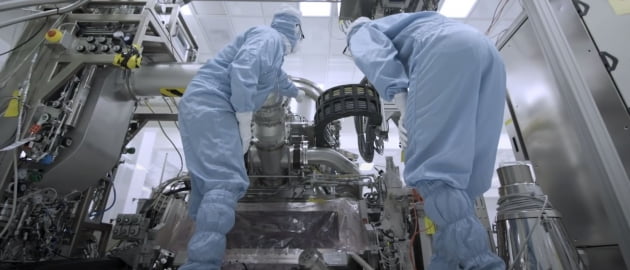
Employees who assemble EUV exposure equipment. Home page capture
In the future, the number of EUV kits manufactured per year is expected to continue to increase. This is because the technology of the equipment parts manufacturers ASML and EUV is growing together. An official from the semiconductor industry explained: “A few years ago, ASML’s manufacturing period was longer than it is now.”
Reporter Hwang Jeong-soo [email protected]