[ad_1]
Resource efficient car production does not use paper or packaging, aluminum and polymers are produced in a closed cycle process and it will be the first new Audi to be developed without any physical prototypes. The world premiere of the new Audi e-tron GT will take place in early 2021, but production is already underway.
Production at the Neckarsulm plant in Germany begins with Audi’s most powerful electric car, the e-tron GT, and the process at Audi’s Böllinger Höf unit is no less unique than the car itself, as no car with the four-ring logo has been ready for production. production.
“The Nekarsulmas plant is already dominated by network-operated hybrid models, as it produces the most electrified versions of the Audi hybrid and the A6, A7 and A8 network-operated hybrids. The Audi e-tron GT will be the first fully electric model to It will be produced at the plant in Germany, which will make it another big step into the future, ”says plant manager H. Stettner.
Production of the Audi e-tron GT
The powertrain concept of this Gran Turismo model is not only sustainable: the entire production process at Böllinger Höfe is carbon neutral. 2020 At the beginning of the year, the entire Nekarsulmas plant started using green electricity, and the heat required for production is supplied by a biogas thermal power plant. Audi uses emission credits from certified climate protection projects to cover the emissions that are currently unavoidable from renewable energy sources.
“After the Brussels and Győr plants, Böllinger Höf is now Audi’s first carbon-free production line in Germany. This is a big step for the Nekarsulm plant and another step towards achieving it by 2025. All of our plants around the world would be carbon neutral, ”says Peter Kössler, board member of Audi’s production and logistics division, summarizing main objective of Audi’s Mission: Zero program.
The Environmental: Mission: Zero Environmental program covers many production and logistics processes to reduce environmental pollution efficiently and sustainably. The main objectives are carbon reduction, resource efficiency, biodiversity and innovative solutions for the use of water.
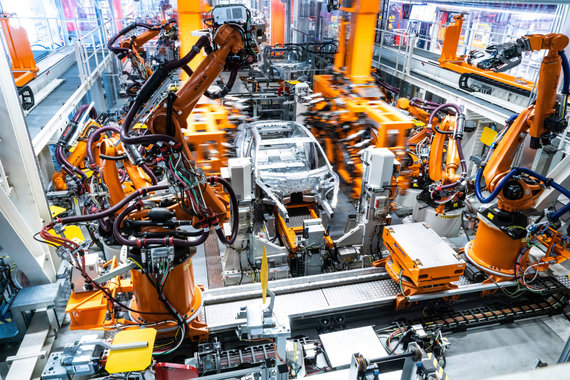
Photo of the manufacturer / Division of Böllinger Höf that produces Audi
Green logistics
To produce neutral emissions, Audi adopts consistent and value-added solutions, so logistics is no less important than the production of the car itself. All train transport at the Nekarsulm plant has no impact on the climate, and the locomotives running between the car park and the plant run on compressed gas or electricity.
Audi experts have also pointed out that the largest car carriers use biomethane gas trucks for transportation. Parts needed for the plant are also delivered by two long-distance LPG trucks.
The closed wheel production cycle protects the environment
The factory also saves materials used in production and recycles raw materials. The best example of this is the “Closed aluminum wheel” cycle used for the recycling chain of the aluminum waste generated in the stamping shop during the production of the body sections of the Audi e-tron GT. The body parts are highly convex, forming the efficient wheel arches of the e-tron GT, emphasizing the quattro gearbox and using state-of-the-art technology for extremely sophisticated aluminum processing. The closed cycle of aluminum treatment saves the plant several thousand tonnes of CO2 emissions each year by returning classified aluminum scrap to the supplier, where it is recycled and reused at the Audi plant.
But green thinking isn’t limited to aluminum. Polymers are recycled under the motto “turning old into new”. In pilot projects A6 and A7, the polymer waste generated during production is sorted, shredded and recycled into a special fiber, which is then used for production in 3D printers. Böllinger Höfe, the team responsible for 3D printing, is implementing highly customized enhancements based on employee feedback; More than 100 of these improvements are used in the production of the Audi e-tron GT. The goal of the recycling project is to create a perfect closed polymer circle.
Systematic resource conservation
The closed production cycle is used not only to save raw materials. The e-tron GT is the first Audi model to be developed without the use of physical prototypes. The entire production sequence has been virtually tested, using self-developed software and virtual reality applications, which are now successfully used in serial production of the model. Some special containers have also been created virtually to transport vulnerable parts without the use of physical prototypes. This saves not only metal, but also packaging for the protection of parts.
The most important goal is to do without waste and paper. Paper is almost no longer used on body production and assembly lines. New projects, like a service program, allow you to avoid the use of traditional records and also help save paper. The logistics department is now testing digital labels, which will replace the paper stickers on the shelves of the container parts.
Not only is this extremely energy efficient, it will also allow labels to be quickly reprogrammed as changes occur, a key advantage over traditional disposable labels. The Audi project team is also working with suppliers to find additional solutions to systematically reduce packaging and consequently waste.
A combination of smart production and precise craftsmanship
Böllinger Höf branch, where since 2014. The Audi R8 has always stood out for its high quality standards, powerful models and passion for every detail. The facilities adapted for the production of small sports cars, which are part of the Audi Nekarsulmas plant, were expanded and renovated in 2019 by installing new production lines and adapting them to the production of the Audi e-tron GT. So here are now two of Audi’s most powerful and fastest production models.
“Production of two technically completely different cars on one assembly line is a completely unique group practice,” says Wolfgang Schanz, Production Manager. “The integration of the four-door electric coupe into our small-scale production line has transformed Böllinger Höfe into a highly flexible, high-tech production line that has retained its small production characteristics.”
Buyers will be able to order the first all-electric Gran Turismo model immediately after its world premiere early next year.
[ad_2]