[ad_1]
Original title: Take a nap around the moon to “go home”
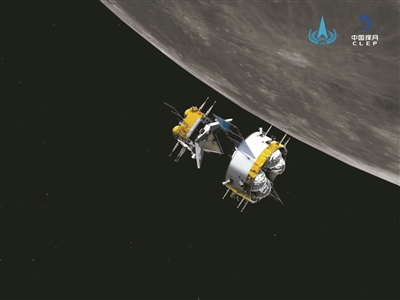
The Chang’e-5 probe docking assembly was successfully detached. The image shows the simulation diagram of the orbital return set separated from the ascendant.

The simulation diagram before separating the orbital return set from the ascendant. (Photo by Xiao Huanhuan)
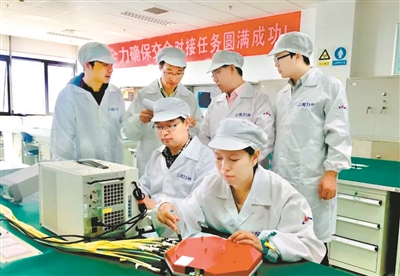
25 scientific researchers from the Second Academy of Aerospace Science and Technology (Photo by Feng Qiuyu)
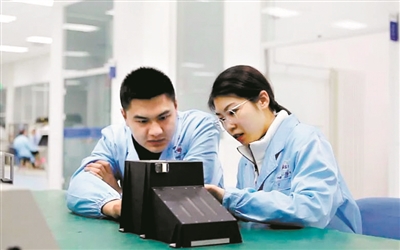
25 scientific researchers from the Second Academy of Aerospace Science and Technology (Photo by Feng Qiuyu)
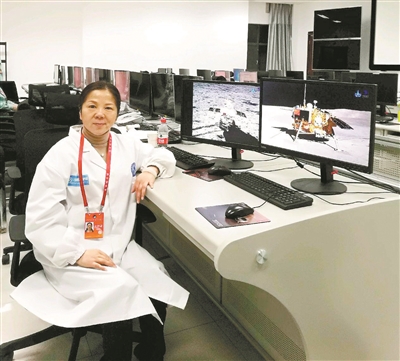
Zhang Yuhua, deputy commander of the Chang’e-5 probe (photo by Xiao Huanhuan)
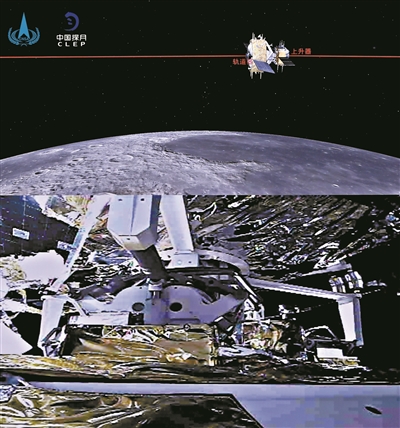
The combination of the Chang’e-5 ascendant and the orbiter’s return completes the rendezvous and docking scene.
At 5:42 a.m. on December 6, the Chang’e-5 ascender was successfully reunited and docked with the orbiter’s return assembly, and the lunar sample container was safely transferred to the return at 6:12 p.m. . This is the first time that China’s spacecraft has achieved a lunar orbital rendezvous and docking point.
At 12:35 on December 6, the Chang’e-5 orbiter’s return assembly successfully separated from the ascendant and entered the moon’s hold phase, ready to return to earth.
Among the many highlights of this mission, the first unmanned automatic encounter and the docking and transfer of samples in lunar orbit are undoubtedly one of the highlights. Among them, the claw mechanism, the lunar orbit microwave radar and the inertial measurement unit are assisting tasks. The central instrument of success, this newspaper will explain you in detail.
By Xiao Huanhuan and Feng Qiuyu, Guangzhou Daily Journalists, Correspondents Wang Junyan, Xu Tong, Zang Jiaxiang, Zhang Bingyao, Lu Zhe, Wu Yongjiang, He Yi, Chen Baojuan
Image source: China National Space Administration (except signature)
Aspect 1:
Berthing and transfer
The world’s first “claw clamping method”
According to experts, starting from when the ascendant enters the orbit around the moon, through long-range guidance and short-range autonomous control, the orbiter-returner assembly gradually approaches the ascendant, capturing the ascendant with claws. and completing the meeting and docking. So what is the “claw clamping method”? What are the highlights of this appointment?
“The claw clamping mechanism has the advantages of light weight, reliable catch, simple structure and high coupling precision. By adding a connecting rod and ratchet transfer mechanism, the integration of the automatic transfer and coupling functions is realized. These design concepts are the first in the world. ” China said Zhang Yuhua, deputy commander of the Chang’e-5 probe of the Eighth Academy of Aerospace Science and Technology Group. “Claws, to put it vividly, are like the action of holding a stick in our hands. When we apply force in two directions, we can hold the stick firmly in our hands.” China Aerospace Science and Technology Group 8th Chang’e Orbiter Technical Assistant Academy 5 According to Hu Zhenyu, the person in charge, the coupling mechanism used by the detector is made up of 3 sets of K-shaped claws. the ascender, simply align the three connecting rods on the connecting surface and tighten the claws to achieve it. The close connection of the two devices.
“The moon’s orbit is delayed relative to the earth’s orbit, which requires very high punctuality, and docking and transfer tasks must be completed at once,” explained Liu Zhong, technical director of the docking organization. and Sample Transfer Subsystem of the Eighth Academy of China Aerospace Science and Technology Corporation: “Docking All steps must be completed in 21 seconds, capture in 1 second, correct in 10 seconds, and lock in 10 seconds. To do this, we have made 35 failure plans, from inception to encounter and docking, all controlled automatically. “
Aspect 2:
“Docking wizard”
Microwave radar is reliable and powerful
The Chang’e-5 docking and meeting microwave radar developed by the 25th Institute of the Second Academy of China Aerospace Science and Industry Corporation, as an “assistant” for medium and long-range measurement, successfully guided the completion of the Chang’e-5 rendezvous and docking mission and played a critical role.
The microwave radar is a pair of products consisting of a main radar and a transponder, which are installed on the Chang’e-5 orbiter and ascendant respectively. When the orbiter and ascendant are about 100 kilometers apart, the microwave radar begins to operate, continuously providing the navigation control subsystem with the relative motion parameters between the two spacecraft and conducting two-way communication. The two spacecraft adjust their flight attitudes based on the radar signal until the orbiter’s docking mechanism captures and locks the ascendant. Subsequently, the lunar soil sample in the ascendant was transferred to the returner.
The meeting and coupling of the orbiter and the ascendant is a complex “big chase to small” force process with huge differences in volume, which requires greater precision in the microwave radar angle measurement. He Zhongqin, director of the microwave radar project designer, introduced that microwave radar is mainly used in the medium and long range range of 100 kilometers to 20 meters, and the improvement of precision has greatly improved the chances of a precise coupling.
Also, the elevator equipped with the transponder for docking will inevitably form dust when the moon falls. To ensure safe travel across the moon, the designers installed a dust cover made of special materials on the transponder, “like wearing With glasses, Chang’e’s clairvoyance will not become myopia,” said Ji Bo, designer of 25 institutes.
Aspect 3:
“Traffic team”
Contract Acceleration Measurement Tasks
The “Inertial Measurement Equipment” provided high-precision acceleration information for the “Chang’e-5” with stable and reliable performance at all times, laying the foundation for the success of this meeting and docking.
Acceleration during encounter and docking is only one ten thousandth of the detector’s maximum acceleration during its take-off process. The combination of high-precision accelerometers can achieve an accurate measurement of small accelerations. The “inertial measurement equipment” consisting of a combination of high precision accelerometers, flexible quartz accelerometers and I / F conversion circuits developed by China Aerospace Science and Industry Group Co., Ltd. will allow “the space of the hand” don’t “pass”.
The high-precision accelerometer combination that mainly implements the acceleration measurement is the “captain” of this “inertial measurement equipment”, which is primarily responsible for the translation of the probe in the phases of earth-moon transfer, flight circumlunar, lunar orbital encounter and docking, and moon-ground transfer Acceleration measurement for smooth and precise maneuvering control of the probe during orbital flight and encounter and docking. The newly added internal shock absorber is like adding a set of vibration absorbing and isolating “cushions” to the combination, which can withstand large shocks and vibrations in the external environment.
The flexible quartz accelerometer is a key sensor for sensitive acceleration, and the I / F conversion circuit can convert the current signal output of the accelerometer into a digital pulse signal suitable for computer processing. “The signal conversion process is like using a balance and weights to ‘weigh’ the signal. The change in acceleration is large and the actual signal changes too much, so a large ‘weight’ is needed. Chief designer of the I / F conversion circuit Zhao Hongli described it.
Aspect 4:
Photo artifact
Perfect presentation of the “hug” process
The dual spectrum infrared and visible surveillance camera developed by the Control Institute of the Eighth Academy of China Aerospace Science and Technology Corporation Ltd. perfectly presents the “hug” process of the orbiter and ascendant.
The dual spectrum surveillance camera on the Chang’e 5 is a professional camera gadget. This camera integrates infrared and visible light images. Infrared and visible light sensors obtain image data through their respective optical lenses. Freely switch between two shooting modes to capture infrared and visible light images separately or simultaneously.
“This is the equivalent of adding a night vision device to an ordinary camera. Even if the rendezvous and docking process occurs on the back of the moon and it cannot receive sunlight, we can record the whole process with an infrared camera.” Zheng Xunjiang, Eighth Control Institute Optical Navigation Expert Introduced: “And in the case of light, if the light is too strong, the photos taken by the visible light camera may also be overexposed, which affects the effect of With this dual-spectrum camera, you can ensure that all day long, Recording the rendezvous and docking process in bright light conditions also allows the audience to see the space from the perspective of infrared lenses. “
The camera has a resolution of 2048 × 2048 in the visible spectrum and a resolution of 640 × 480 in the infrared spectrum. On this basis, it also makes simultaneous infrared and visible light images, thus providing a high definition visual experience to audiences on earth. .
Looking to the future: 77 locomotives will accompany the “Five” who return home
The R&D team of the Sixth Academy of Aerospace Science and Technology Group custom-built two 3 new engines for the probe, known as the “artifact” of Chang’e 5’s return to the moon.
The three propulsion subsystems used for landing and returning the Chang’e 5 consist of 77 orbital attitude control engines of different sizes and performance. Among them, the research and development team of the Sixth Academy of Aerospace Science and Technology Group has designed two models of three new engines for the probe, known as the “artifact” of the return of Chang’e 5 to the moon.
Two of the 3000N engines will drive the Chang’e-5 orbiter and ascendant respectively. A 3000N motor in the orbiter provides thrust for earth-moon transfer, intermediate lunar-earth transfer correction, braking near the moon, and acceleration from the moon, while another 3000N motor in the ascendant will provide thrust for lunar liftoff. It is equivalent to a miniature launch vehicle on the moon. A 7500N variable thrust engine will complete the lunar soft landing mission of the probe’s landing complex.
In developing the 3000N engine, the R&D team of the Sixth Academy of Aerospace Science and Technology Group attaches great importance to the environmental adaptability of the engine. While improving engine performance, it controls the engine thrust chamber temperature, taking full account of adequate and reliable cooling to ensure long life and reliable engine operation. Compared to other types of motor components, parts processing on the 7500N Variable Thrust Motor Flow Regulator requires extremely high precision, and the tolerances are all in microns, which is 1/80 of a hair, only in a flow adjustment cone. There are 8 machining difficulties with micron tolerances.