[ad_1]
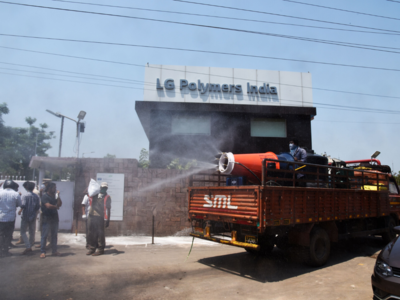
NEW DELHI: days after the gas leak accident at a polymer plant in Visakhapatnam, the National Disaster Management Authority (NDMA) has issued a set of guidelines on the safe restart of industries after closure. These guidelines require that the first week after the restart be considered a trial period in which all security protocols must be ensured and high production goals are avoided.
“To minimize risk, it is important that employees working on specific equipment are sensitized and aware of the need to identify abnormalities such as unusual sounds or odors, exposed wires, vibrations, leaks, smoke, abnormal wobble, irregular grinding, or other potentially dangerous signs indicating the need for immediate maintenance or, if necessary, shutdown, “set the NDMA guidelines shared by its member secretary with all states / UT on Saturday.
NDMA told states / UT that due to several weeks of closure and closure of industrial units, some of the operators may not have followed established standard operating procedures, as described in the NDMA guidelines on chemical disasters issued in 2007 ; Strengthening security for the transport of tankers POL, 2010; and Manufacture, Storage and Import of Dangerous Chemicals Rules, 1989 under Environment Protection Act.
“As a result, some of the manufacturing facilities, pipes, valves, etc. They may have residual chemicals, which can pose a risk. The same is true for storage facilities with hazardous chemicals and flammable materials, “he noted.
Many energy sources can be dangerous to operators / supervisors servicing or maintaining electrical, mechanical, or chemical equipment.
And when machinery and heavy equipment are not regularly maintained, they can become dangerous to operators / engineers, said NDMA.
Claiming that managing rapid response becomes challenging when an unexpected event occurs, the NDMA unveiled a series of guidelines on the safe restart of industries on Saturday.
According to these guidelines, the first week after restarting the unit, should be considered as the trial period or trial run and avoid high production. To minimize risk, employees working on specific equipment should be sensitized and aware of the need to identify abnormalities such as strange sounds or odors, exposed wires, vibrations, leaks, smoke, abnormal wobble, irregular grinding, or other potentially dangerous signs indicating need for immediate maintenance or, if necessary, shutdown.
All equipment must be inspected according to security protocols during the restart phase. In the event that the industry has any difficulty in handling crucial crucial links that may be critical to their safe operation, they should contact the local district administration for specific assistance. State governments will also ensure that the off-site disaster management plan of the respective Major Accidental Risk Units (TACs) is up-to-date and readiness to implement them is high.
1. The unit may be facilitated to perform its operations end-to-end, in the general interest of industrial security.
2. Storage facilities can be inspected for signs of spills, wear and tear during closure.
3. The chemical stability of HAZMAT chemicals in storage should be verified prior to use for any process.
4. Supply lines / valves / conveyor belts should be checked for signs of damage / wear
5. For the safety of manufacturing processes, a full safety audit of the entire unit should be performed before activities begin.
6. Cleaning of pipes, equipment and discharge lines: mechanical cleaning must be ensured followed by air / water purging.
7. Many process units handle fuels or toxic substances (or both), whose leakage could cause disasters, damages or economic losses. To avoid the occurrence of such incidents, it is necessary to confirm that the plant meets the required tightness before commissioning.
8. The service test should be performed for all water, compressed air, and steam piping and equipment with normal operating fluids. The system is first pressurized with operating fluids and then checked for leaks. Vanishing points found during the test are retightened.
9. All vacuum systems must be leak tested.
10. Trial tests will be carried out before full production starts with full human resources.
11. Industrial units must ensure the provision of 24-hour emergency teams / professional technical teams provided with MAH and the MAH group must have an extended coverage of 200 km to reach transport accident sites in search of help
12. For the safety of the workers, the industrial units must guarantee the disinfection of the factory facilities. They must also undergo health checks at the entrances.
.
[ad_2]